Are you ready to unleash your inner tech-savvy designer? Craft your very own custom computer monitor. The future of DIY monitor builds is here, thanks to small CNC laser cutters and Filescnc’s designs. Say goodbye to the one-size-fits-all approach and hello to personalized computer setups that reflect your style and preferences.
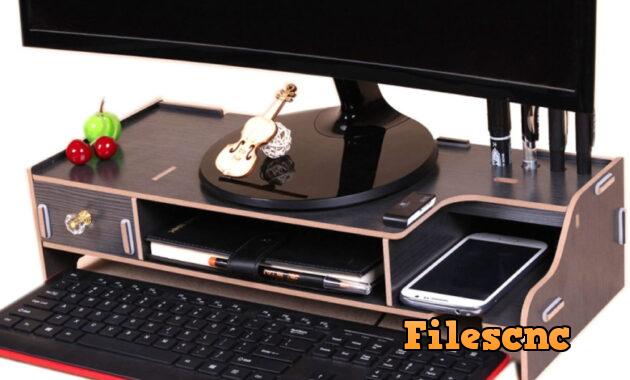
In 2024, computer monitor customization is set to transform, with Filescnc leading the way. Their extensive library of laser-cut designs lets you create a monitor that looks stunning and fits perfectly with your tech setup. No more settling for off-the-shelf options. It’s time to craft a monitor that’s truly your own.
Key Takeaways
- Explore the exciting world of laser-cut computer monitor customization in 2024.
- Discover how small CNC laser cutters are revolutionizing the DIY monitor build industry.
- Learn how Filescnc’s innovative designs can help you create a one-of-a-kind computer setup.
- Unleash your inner designer and take control of your computer’s aesthetic.
- Embrace the future of personalized technology with laser-cut monitor builds.
Understanding Small CNC Laser Cutting Technology
The world of laser cutting has changed a lot. Now, small CNC laser systems lead this change. These tools are key in many fields, from making custom computer monitors to detailed designs. Let’s explore what makes these systems tick.
Basic Principles of Laser Cutting Operations
Laser cutting doesn’t touch the material. It uses a strong laser beam to cut or engrave many materials. This includes acrylic, glass, and metal. The laser melts or vaporizes the material, making complex designs possible with great accuracy and speed.
Components of Modern CNC Laser Systems
Small CNC laser systems have a few main parts. These are the laser source, motion control, and computer interface. The laser source, like a CO2 or fiber laser, creates the high-energy beam. The motion control system moves the laser or workpiece to follow the cutting path. The computer interface lets users design and control the cutting process with CAD/CAM software.
Power Requirements and Specifications
The power needed for small CNC laser systems varies. It depends on the material and cutting depth. These systems usually use 40-100 watts. This power is enough to cut through materials often used in computer monitor builds, like acrylic, glass, and thin metal.
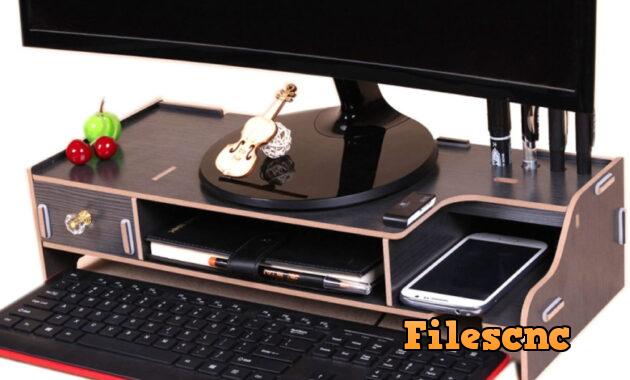
“The versatility and precision of small CNC laser cutting systems have revolutionized the way we approach custom computer monitor builds and design projects.”
Benefits of Custom Monitor Builds in 2024
Exploring custom monitor builds in 2024 opens up new possibilities for personalization. You can create a unique workspace that stands out. This is something off-the-shelf models can’t offer.
One key benefit is the ability to customize size, shape, and look. Whether for a DIY project or a personalized workspace, laser-cut monitors let you design your dream display. It fits perfectly with your setup.
Custom monitors can also save you money. By designing and making them yourself, you can use materials wisely. This way, you get a display that fits your budget and meets your needs.
“The ability to customize every aspect of my monitor has been a game-changer for my productivity and overall workspace satisfaction.”
Custom monitors also offer unique features not found in standard models. You can add special lighting or ergonomic adjustments. The only limit is your creativity and technical skills.
The appeal of custom monitor builds in 2024 is growing. It’s perfect for those who want to enhance their computing experience. As DIY projects and personalized workspaces grow, so does the interest in custom monitors.
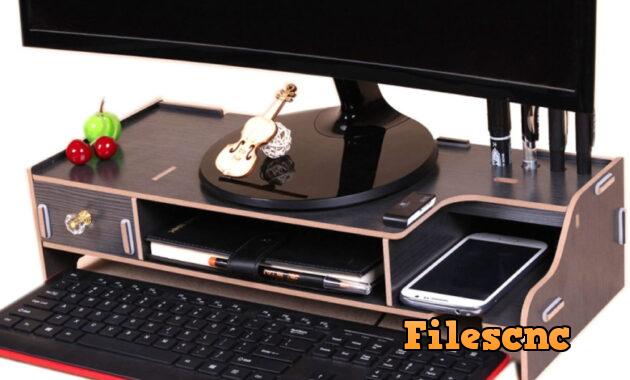
Essential Materials for Laser Cut Computer Monitor Projects
Choosing the right materials is key when making your own laser-cut computer monitor. You’ll need transparent panels for the display and strong metal parts for the structure. Each part is important for the final look and function of your custom monitor.
Acrylic vs. Glass Options
Deciding between acrylic sheets and tempered glass is a big choice. Acrylic is light, shatter-resistant, and affordable. Glass gives a high-end look but costs more. Think about what you need for your project.
Metal Components and Considerations
The metal components like the frame and stand are crucial. Choose metals like stainless steel or aluminum for strength and durability. They help your monitor last longer.
Protective Coatings and Finishes
Adding protective finishes is vital to keep your monitor safe from damage. Look into anti-glare coatings and decorative finishes. They make your monitor look great and last longer.
“The right materials can transform a simple laser-cut project into a professional-grade, visually stunning computer monitor.”
By picking the right acrylic sheets, metal components, and protective finishes, you’ll make a monitor that looks amazing and works perfectly. It will show off your design and skill.
Laser Cut Computer Monitor small cnc laser cutter Setup Guide
Creating a custom computer monitor with a laser cutter needs careful setup. First, make sure your workspace is ready and safe. Here’s how to set up your small CNC laser cutter for a smooth monitor project.
Workspace Preparation
Make a clean, well-ventilated, and organized workspace. Place the laser cutter on a stable, level surface. Keep it away from flammable stuff and blockages. Have all tools like measuring tapes, clamps, and safety gear ready and within reach.
Safety First
When using a laser cutter, safety comes first. Wear the right protective gear like safety glasses, gloves, and a mask. Learn about the laser cutter’s safety features and how to stop it quickly if needed.
Initial Calibration
Do a detailed calibration before starting your project. Adjust the beam, focus the laser, and check the cutting depth and power. Use the maker’s guide or ask experts to get the best cuts.
Step | Description | Recommended Tools |
---|---|---|
1. Workspace Preparation | Create a clean, well-ventilated, and organized work area for the laser cutter. | Measuring tape, clamps, cleaning supplies |
2. Safety Equipment | Equip yourself with the necessary personal protective equipment (PPE). | Safety glasses, gloves, respirator mask |
3. Laser Cutter Calibration | Adjust the beam alignment, focus, and power settings for optimal performance. | Manufacturer’s instructions, alignment tools |
By following these steps, your small CNC laser cutter will be ready for your custom computer monitor project. Next, we’ll look at design software and file prep.
Design Software and File Preparation
Creating custom monitor designs is easier with the right software. CAD (Computer-Aided Design) offers many tools to help. You can use AutoCAD, SolidWorks, Fusion 360, or SketchUp to bring your ideas to life.
CAD Tools for Monitor Design
AutoCAD and SolidWorks are top choices for detailed designs. They have features for 2D and 3D modeling. Fusion 360 and SketchUp are great for beginners because they are easy to use.
It’s important to learn how to use your CAD software well. This ensures your design works well with laser cutting. You’ll need to know about vector graphics for clean cuts.
File Format Compatibility
After designing, make sure your file works with your laser cutter. DXF and SVG are the best formats for laser cutting. These formats keep your design clear and work well with your CNC laser cutter.
Using the right software, mastering vector graphics, and choosing the right file formats are key. This will help you create amazing laser-cut monitor projects. Preparation is key, so explore tools and resources to make your design a reality.
CAD Software | Key Features | File Formats |
---|---|---|
AutoCAD | Comprehensive 2D and 3D modeling, industry-standard | DXF, DWG |
SolidWorks | Advanced 3D modeling, simulation, and engineering tools | SLDPRT, SLDASM, SLDDRW |
Fusion 360 | Intuitive interface, cloud-based collaboration, CAM integration | DXF, STL, STEP |
SketchUp | User-friendly 3D modeling, emphasis on rapid prototyping | SKP, DXF, STL |
“With the right design software and file preparation, the possibilities for custom laser-cut monitor projects are truly endless.” – Filescnc
Safety Measures and Precautions
Working with laser cutting technology needs careful attention to safety. When you start your custom monitor build, remember to wear protective gear and ensure good air flow. This keeps you and your workspace safe.
Wearing the right laser safety gear is key. Get safety goggles that block the laser beam’s intense light. Also, use protective gear like heat-resistant gloves to protect your hands from heat and debris.
- Laser safety goggles
- Heat-resistant gloves
- Well-ventilated workspace
Good ventilation requirements are vital for a safe work area. Make sure your laser cutter is in a place with plenty of air flow. This helps get rid of any fumes or particles made during use. Think about adding an exhaust system or air filter to keep the air clean.
Safety Measure | Importance |
---|---|
Laser safety goggles | Protect your eyes from the intense laser beam |
Heat-resistant gloves | Shield your hands from heat and debris during cutting |
Proper ventilation | Ensure a healthy, clean working environment by removing fumes and particles |
Table of Contents
“Safety should always be the top priority when working with powerful tools like laser cutters. Prioritize protective gear and a well-ventilated workspace to ensure a successful and secure project.”
Following these safety steps lets you use your small CNC laser cutter safely. It keeps you and your area safe. Enjoy the process of making your custom monitor with laser cutting technology.
Step-by-Step Cutting Process Overview
To get the most out of your laser-cut computer monitor project, you need to know how to position materials, set laser power, and adjust cutting speed. This guide will show you the key steps for precision, efficiency, and a perfect finish.
Material Positioning Techniques
Getting your material in the right spot is key for laser cutting success. First, clamp your workpiece firmly to keep it steady. Try different clamping ways and spots to find the best for your materials and design.
Make sure your workpiece is perfectly aligned. Any small mistake can cause bad cuts or misalignments.
Power Settings and Speed Adjustments
Finding the right mix of laser power settings and cutting speed optimization is vital for clean cuts. Start by testing on scrap to find the best settings for your material. Then, tweak these settings to get the cleanest cuts.
Getting the right mix of material positioning, laser power settings, and cutting speed optimization is crucial. It can make your laser-cut monitor look professional or not. Take your time to experiment and improve your skills.
Assembly Techniques and Best Practices
Building a custom computer monitor is an exciting adventure. Now, it’s time to put everything together. We’ll focus on the art of assembly, where precision and detail are key. From managing cables to adding the final touches, we’ll make your monitor stand out.
Organizing wires might seem hard, but don’t worry. Our cable management tips will make your monitor look sleek. By routing cables smartly and using cable clips, you’ll avoid messy tangles. This will give your monitor a clean, professional look.
The final touches are what make your monitor truly special. You can choose a matte or high-gloss finish to add sophistication. With careful attention, you’ll turn your laser-cut monitor into a masterpiece. It will be a stunning addition to your desk.
FAQ
What is the latest trend in custom computer monitor builds?
In 2024, the trend is using small CNC laser cutters to make your own monitor. DIY fans love making unique workspaces with their own designs.
How do small CNC laser cutters work for monitor projects?
These cutters use a laser beam to cut through materials like acrylic and glass. They make custom shapes and designs that standard monitors can’t match.
What are the key benefits of building a custom laser-cut monitor?
Building your own monitor lets you personalize it. It’s also cost-effective and can have unique features. You can make it fit your style perfectly.
What materials are typically used for laser-cut monitor projects?
Acrylic and tempered glass are common for the front panel. Metal like aluminum or steel is used for the frame and stand. Finishes and coatings add durability and look.
How do I set up a small CNC laser cutter for monitor projects?
First, set up a safe workspace and install safety gear. Then, calibrate the laser cutter. A step-by-step guide can help you do it right and safely.
What design software is best for creating laser-cut monitor plans?
CAD tools like AutoCAD and SketchUp are great for designing monitors. Make sure the software works with your laser cutter. Sites like Filescnc have designs ready to use.
How can I stay safe when using a small CNC laser cutter?
Safety is key. Wear proper gear, ensure good air flow, and follow safety rules. This prevents accidents and keeps you safe while cutting and assembling.
What are the key steps in the actual laser cutting process?
Position materials carefully, adjust power and speed, and make clean cuts. Learning these steps helps you make high-quality monitor parts.
What are the best practices for assembling a laser-cut monitor?
Use the right assembly techniques and add finishing touches. This turns your parts into a sleek display. Guides and best practices help you achieve a stunning monitor.