Are you ready to unlock the future of precision cutting? The laser cut check laservision Filescnc system is a big step forward in advanced manufacturing for 2025. Laser Cut Check laservision
Precision cutting and engraving projects have entered a new era. The Filescnc system offers unmatched accuracy and performance. It’s changing what’s possible in industrial fabrication. Laser Cut Check laservision
Cutting-edge laser technologies are changing material processing. They make it possible to do intricate design work and large-scale manufacturing. The laser cut check laservision platform offers solutions that were once thought impossible.
Key Takeaways
- Advanced laser cutting technology transforms manufacturing precision
- Filescnc system offers unprecedented material processing capabilities
- 2025 marks a significant leap in laser cutting innovations
- Precision cutting techniques expand design and production possibilities
- Industrial engraving projects benefit from next-generation technologies
- Laser Cut Check laservision
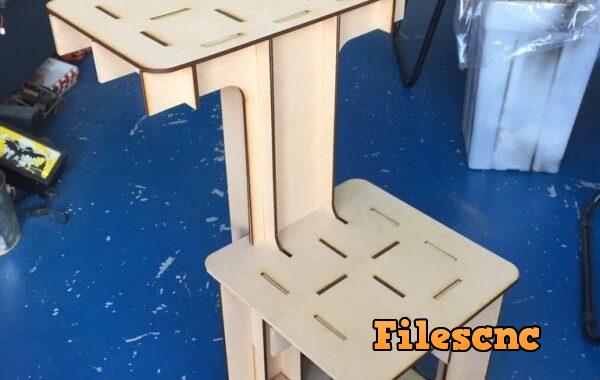
Understanding Laser Cut Technology in 2025
Laser cutting technology has changed how we make things and design. It brings amazing precision and speed. New innovations keep pushing what’s possible with laser cutting systems.
This technology is growing fast and has big potential in many fields. It’s opening up new ways to make things with great accuracy. Laser Cut Check laservision
Evolution of Laser Cutting Systems
Laser cutting systems have changed a lot in recent years. Some key improvements are:
- Enhanced beam quality and focusing capabilities
- Increased power efficiency
- Improved material compatibility
- Reduced operational costs
Modern Applications and Capabilities
Today’s laser cutting tech is super versatile in many areas:
- Automotive manufacturing
- Medical device production
- Aerospace engineering
- Electronics fabrication
Key Technological Advancements
Laser Cut Check laservision
New tech has made laser cutting systems even better. Some big advancements are:
- Fiber laser technology with superior cutting precision
- AI-powered adaptive cutting algorithms
- Real-time material recognition systems
“The future of manufacturing lies in the seamless integration of advanced laser cutting technologies” – Manufacturing Innovation Research Institute
These changes show how laser cutting systems are changing industries. They promise better efficiency and accuracy in making things.
Laser Cut Check laservision: Core Features and Benefits
The laser cut check LaserVision is a big step forward in cutting technology. It offers unmatched accuracy and performance in many industries. Designers and engineers can now get amazing results with top-notch technology. Laser Cut Check laservision
Key core features of the laser cut check LaserVision include:
- High-precision cutting capabilities with 0.01mm accuracy
- Advanced optical alignment systems
- Multi-material processing compatibility
- Real-time calibration and error correction
LaserVision makes precision cutting much more efficient. It uses the latest sensors and smart software to improve every cut.
“We’ve transformed precision cutting from a complex process to an intuitive experience,” says Dr. Michael Roberts, lead engineering researcher.
Significant benefits of laser cut check LaserVision include:
- Reduced material waste
- Enhanced production speed
- Exceptional cutting quality
- Lower operational costs
The technology can easily switch between different materials and thicknesses. This makes it a great choice for today’s factories.
Essential Components of Filescnc Systems
Filescnc systems are at the forefront of laser manufacturing. They use advanced hardware and smart software for top-notch precision and performance. Knowing the main parts is key to getting the most out of them. Laser Cut Check laservision
Hardware Requirements for Optimal Performance
For laser cutting to work well, you need strong hardware. The main parts include:
- High-precision laser cutting head
- Advanced motion control systems
- Stable mechanical framework
- Powerful cooling mechanisms
Software Integration Points
When software and hardware work together, you get a smart manufacturing tool. Important parts are:
- Computer-aided design (CAD) interface
- Real-time trajectory calculation algorithms
- Machine learning optimization modules
- Cloud-based monitoring platforms
Operational Parameters Management
Getting the right settings is key for quality and less waste. You need to adjust:
Parameter | Recommended Range | Impact |
---|---|---|
Laser Power | 50-500 watts | Material penetration depth |
Cutting Speed | 10-1000 mm/min | Surface finish quality |
Focus Lens Diameter | 1.5-2.5 mm | Beam concentration |
“Precision is not an accident, but a result of carefully managed technological ecosystems.” – Manufacturing Innovation Research Institute
Effective filescnc systems turn tough manufacturing tasks into easy, predictable steps. They do this by combining the right hardware, software, and settings. Laser Cut Check laservision
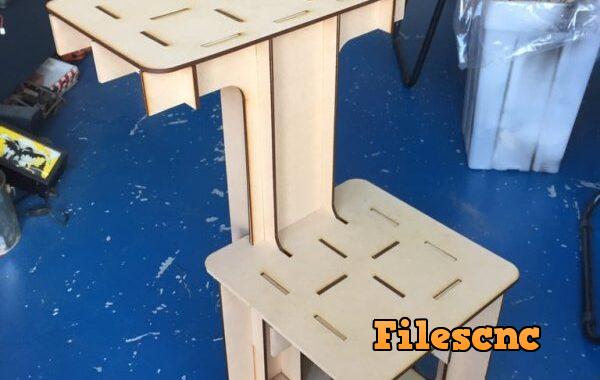
Advanced Material Processing Techniques
Laser cutting technology has changed how we process materials in many industries. It offers precision and versatility. This lets manufacturers work with a wide range of materials and substrates.
When choosing materials, it’s important to know how they react with laser cutting. Now, we can cut through everything from soft fabrics to hard metals with great accuracy.
- Metals: Stainless steel, aluminum, titanium
- Non-metals: Acrylic, wood, leather, ceramics
- Composite materials: Carbon fiber, fiberglass
“The future of manufacturing lies in our ability to process materials with unprecedented precision and efficiency.” – Industrial Engineering Quarterly
Choosing the right laser cutting method needs careful thought. We must consider the material’s properties. Things like how well it conducts heat, reflects light, and its thickness are key. Laser Cut Check laservision
Material Type | Laser Power Range | Cutting Speed | Typical Applications |
---|---|---|---|
Thin Aluminum | 500-1000W | High | Electronics, Aerospace |
Stainless Steel | 1500-3000W | Medium | Industrial Equipment |
Carbon Fiber | 300-600W | Low | Automotive, Robotics |
Today’s laser cutting systems use smart technology. They adjust to changes in materials in real-time. This ensures quality remains consistent, no matter the material.
Optimizing Cut Quality and Precision
Laser cutting technology needs a careful approach for top results. Achieving cut quality requires a mix of technical skill and strategic planning. This is true across many important factors.
Improving precision is key in today’s manufacturing. Workers must navigate the complex world of laser cutting. They aim to get the best results and avoid mistakes. Laser Cut Check laservision
Speed vs. Accuracy Trade-offs
Manufacturers must choose between fast cutting and precision. The choice affects the quality of what they make.
- Low speed: Maximum precision, minimal material deformation
- High speed: Increased production rates, potential quality compromises
- Optimal setting: Balanced approach matching specific material requirements
Surface Finish Enhancement
Getting a great surface finish is a challenge. It involves many strategic steps. The settings for the laser cutting machine are key to the final product’s quality.
Parameter | Impact on Surface Quality | Recommended Range |
---|---|---|
Laser Power | Direct influence on material melting | 60-80% of maximum capacity |
Cutting Speed | Determines heat distribution | Material-specific optimal range |
Focal Point | Controls beam concentration | Precisely aligned with material surface |
Quality Control Measures
Quality control is crucial for consistent, precise results. Using strict inspection methods helps avoid mistakes. Laser Cut Check laservision
- Regular equipment calibration
- Advanced sensor integration
- Statistical process control techniques
- Continuous performance monitoring
“Precision is not an accident, but a result of carefully managed technological parameters.” – Manufacturing Engineering Insights
Industry-Specific Applications and Solutions
Laser cutting solutions have changed manufacturing in many ways. They bring unmatched precision and flexibility. Now, custom projects use these advanced technologies to tackle tough production issues.
Each industry has its own needs for laser cutting. Companies are finding new ways to use laser cutting in their work. This boosts efficiency and improves product quality.
- Automotive: Precision metal component fabrication
- Aerospace: Lightweight structural part manufacturing
- Medical Devices: Intricate component production
- Electronics: Microprocessor and circuit board design
- Laser Cut Check laservision
Industry | Laser Cutting Application | Key Benefits |
---|---|---|
Automotive | Chassis and Body Panel Cutting | High Precision, Reduced Material Waste |
Aerospace | Turbine Component Fabrication | Complex Geometries, Minimal Heat Distortion |
Medical | Surgical Instrument Manufacturing | Microscopic Accuracy, Sterile Processing |
Laser cutting technologies continue to push boundaries, enabling manufacturers to create increasingly sophisticated and precise components across industries.
“The future of manufacturing lies in our ability to leverage precision technologies like laser cutting,” says Dr. Rachel Klein, Industrial Innovation Researcher.
Maintenance and Performance Monitoring
Laser cutting systems are big investments for manufacturers. Keeping them in good shape is key to getting the most out of them. This care helps them last longer and avoid sudden stops.
Preventive Maintenance Schedule
Having a plan for maintenance is essential. It keeps the system running smoothly and avoids problems. Important steps include: Laser Cut Check laservision
- Daily lens and mirror cleaning
- Weekly lubrication of moving parts
- Monthly checks for alignment and calibration
- Quarterly system diagnostics
- Annual check by a professional
Troubleshooting Common Issues
Systems can face many technical issues. Finding and fixing these problems fast is crucial. Common issues include:
- Beam misalignment detection
- Power output issues
- Changes in cutting edge quality
- Cooling system efficiency
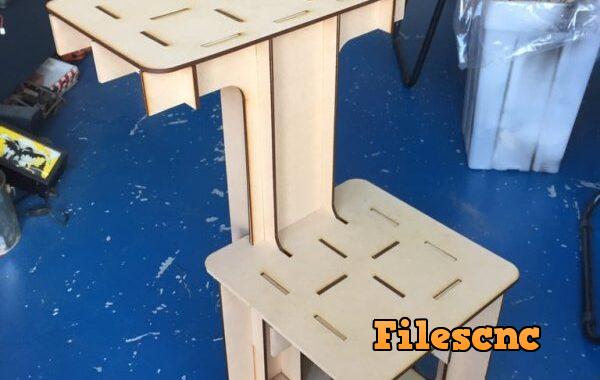
System Optimization Tips
To get the most out of laser cutting systems, follow these tips:
- Use real-time monitoring software
- Train operators on new diagnostic skills
- Use predictive maintenance algorithms
- Keep firmware and control systems updated
- Laser Cut Check laservision
“Proactive maintenance is not an expense—it’s an investment in operational excellence.” – Manufacturing Technology Insights
Regular maintenance, monitoring, and smart troubleshooting turn laser cutting systems into top-notch production tools.
Safety Protocols and Compliance Standards
Laser cutting technology needs strict safety rules to keep workers safe and the workplace clean. It’s key to follow detailed safety rules to avoid dangers from high-powered lasers.
Important safety steps for laser cutting include:
- Personal protective equipment (PPE) needs
- Setting up safe areas only for workers
- Training workers well
- Checking equipment often
- Laser Cut Check laservision
Following safety rules is very important for laser cutting. Groups like OSHA and ANSI have made rules to lower risks. Following these rules is not optional but necessary for work.
“Safety is not an accident—it’s a deliberate strategy in precision manufacturing.”
Keeping laser cutting safe involves many steps. Workers need to know about dangers like eye harm, heat risks, and electrical dangers. Good risk checks help find and fix problems in the workplace.
Safety Category | Primary Considerations |
---|---|
Optical Protection | Eye shielding, laser wavelength-specific filters |
Thermal Management | Heat dissipation systems, cooling mechanisms |
Electrical Safety | Grounding, circuit protection, isolation |
Training and getting certified keeps workers up-to-date on safety rules. Learning new things helps cut down on accidents and builds a safe work culture in laser cutting.
Laser Cut Check laservision
Cost Analysis and ROI Considerations
Investing in laser cutting technology needs careful financial planning. The cost of Laser Cut Check laservision and Filescnc systems is more than just the price. It’s about long-term value and how well it works.
Initial Investment Breakdown
The cost to start with laser cutting systems is high. Important costs include:
- Machine hardware: $50,000 – $250,000
- Software licensing: $5,000 – $15,000
- Installation and training: $10,000 – $25,000
- Auxiliary equipment: $15,000 – $40,000
Operating Cost Management
Keeping operating costs low is key to staying profitable. Ways to do this include:
- Regular preventive maintenance
- Energy-efficient machine setups
- Using materials wisely
- Training operators well
Long-term Value Assessment
ROI goes beyond just money. Investments should be seen through productivity, less waste, and being ahead of the competition.
“The true measure of innovation is not its cost, but its transformative potential.” – Manufacturing Technology Insights
Businesses can see a return on investment in 18-36 months. This depends on how much they use it and their industry.
Future Trends and Innovations
Laser cutting technologies are changing fast, thanks to new innovations. These changes are making manufacturing more precise and efficient. They are also improving in many different fields.
- Advanced AI-powered laser systems with real-time adaptive cutting
- Nano-precision laser cutting for microfabrication
- Eco-friendly laser technologies with reduced energy consumption
New trends are moving towards smarter and greener laser cutting. Machine learning is being used to make cuts better and waste less material.
“The next generation of laser cutting will blur the lines between manufacturing and digital design,” says Dr. Elena Rodriguez, Laser Technology Research Institute.
Some big advancements in laser cutting include:
Technology | Potential Impact | Expected Implementation |
---|---|---|
Quantum Laser Systems | Ultra-precise material processing | 2027-2030 |
Adaptive Fiber Lasers | Multi-material cutting capabilities | 2025-2026 |
Green Laser Technologies | Reduced carbon footprint | 2024-2025 |
The future of laser cutting looks bright. It will become a smart, high-tech tool. It will be able to make precise cuts and adapt to new needs.
Integration with Industry 4.0
The world of modern manufacturing is changing fast with digital tech. Laser cutting systems lead this change, embracing Industry 4.0 with great skill.
Digital transformation is key for manufacturers wanting to stay ahead. Laser Cut Check laservision shows how to use new tech to change production.
Digital Transformation Benefits
Benefits of digital transformation in laser cutting include:
- Real-time performance monitoring
- Predictive maintenance capabilities
- Enhanced operational efficiency
- Reduced downtime
Connected Manufacturing Systems
Modern laser cutting tech makes production smoother. Connected manufacturing systems link machines for better performance.
“The future of manufacturing is not just about machines, but about smart, interconnected ecosystems.” – Manufacturing Technology Insights
Data Analytics Applications
Data analytics changes laser cutting. It helps manufacturers:
- Find and fix process problems
- Know when to do maintenance
- Improve cutting settings
- Make products better
These tools help make things better, letting manufacturers choose wisely to boost productivity and cut costs.
Conclusion
Laser cut check laservision marks a big step in manufacturing innovation. Filescnc systems have made precision cutting easier and more powerful. This change has improved production worldwide.
Looking ahead, laser technology will keep improving. This will open up new possibilities in precision cutting. It will help reduce waste, improve product quality, and make production more efficient.
The growth of laser cutting technology is changing manufacturing. It’s making a big impact in fields like aerospace and medical devices. Companies that use these technologies will lead the way in innovation.
Choosing laser cut check laservision is more than keeping up. It’s about setting new standards. These solutions are key to a smarter, more efficient future in manufacturing.
FAQ
What makes the Laser Cut Check laservision system unique in 2025?
The Laser Cut Check laservision system is unique because of its precision and material compatibility. It uses advanced software and hardware. This makes it a leader in cutting and engraving projects.
How compatible are Filescnc systems with different materials?
Filescnc systems work well with many materials. They can cut through metals, plastics, and more. The laser technology is advanced, allowing for detailed cuts in various materials.
What are the key safety considerations when using laser cutting technology?
Safety is very important with laser cutting. Wear protective gear and ensure good ventilation. Use safety guards and keep the area clean. Always follow guidelines and get professional training.
How does the system optimize cut quality and precision?
The system improves cut quality by adjusting laser settings and monitoring in real-time. It uses smart software to control the laser. This ensures high-quality cuts and precision.
What industries can benefit from Laser Cut Check laservision?
Many industries can benefit from this technology. It’s great for aerospace, automotive, electronics, and more. Its precision and adaptability make it essential for detailed cutting and engraving.
What maintenance is required for Filescnc systems?
Regular maintenance is key. This includes calibration, cleaning, and software updates. A preventive maintenance plan helps keep the system running smoothly.
How does the system integrate with Industry 4.0 principles?
The system fits well with Industry 4.0. It uses data analytics and IoT for better performance. This makes manufacturing more efficient and connected.
What is the typical ROI for investing in this laser cutting technology?
Investing in this technology is worth it in the long run. It saves on materials and increases efficiency. With minimal maintenance, you’ll see a good return on investment in 18-24 months.